What is AQL?
AQL, is also called Acceptable Quality Limit, refers to the maximum allowed range of the number of defects of each grade found in the sample size during random sampling inspection. If the number of defects is within the maximum allowed range, the goods quality will be acceptable, and vice versa.
All defects are in three grades, Critical, Major and Minor, here are some reference criteria for classification:
Critical--The product has any potential unsafe factor, and during use, the defect may cause personal injury to user or person near it. For example, a broken needle in a clothing would scratch or puncture the user, so such a defect should be Critical. Generally, the acceptable range of Critical defect is 0, which means once a Critical defect is found, the batch of goods will not be accepted.
Major--Any defect that would influence the appearance or use function of the product. Major defect would probably result in the situation of being unsaleable or return or exchange of goods. For example, serious scratches on surface of household appliances or too large assembly clearance.
Minor--A kind of slightly defect, but it will neither influence product sales nor use function. A Minor defect may be a small stain or a small dent.
All defects are in three grades, Critical, Major and Minor, here are some reference criteria for classification:
Critical--The product has any potential unsafe factor, and during use, the defect may cause personal injury to user or person near it. For example, a broken needle in a clothing would scratch or puncture the user, so such a defect should be Critical. Generally, the acceptable range of Critical defect is 0, which means once a Critical defect is found, the batch of goods will not be accepted.
Major--Any defect that would influence the appearance or use function of the product. Major defect would probably result in the situation of being unsaleable or return or exchange of goods. For example, serious scratches on surface of household appliances or too large assembly clearance.
Minor--A kind of slightly defect, but it will neither influence product sales nor use function. A Minor defect may be a small stain or a small dent.
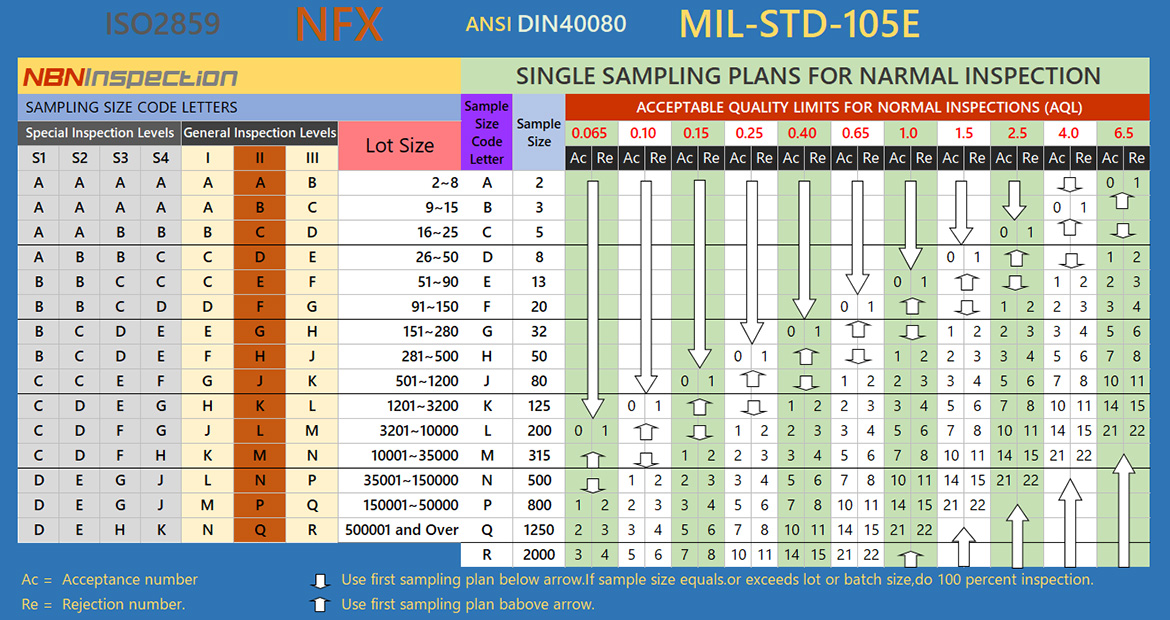
How to use AQL?
The number of acceptable defects is decided by three elements, namely Lot Size, Inspection Level and AQL value. Lot Size is fixed and the other two elements shall be determined by the actual conditions of goods. Different Inspection Levels and AQL values will lead to different number of acceptable defects.
Inspection Level divided into S1, S2, S3, S4, I, II and III, and the further to the right the larger sampling amount, we can choose Level II for general goods.
AQL value divided into 0, …1.0, 1.5, 2.5, 4.0, 6.5, …, and the further to the right the larger number of acceptable defects, which means lower requirements for quality.
Take an example, the quantity of a batch of goods is 7,500 pcs, if we use Inspection Level II, and AQL Critical 0/ Major 2.5/ Minor 4.0.
Step 1: total 7500 pcs can be find the Lot Size is 3201-10000.
Step 2: find the general Inspection Level is L.
Step 3: find L in Sample Size Code Letter and the Sample Size is 200.
Step 4: on the right of this string, AQL Critical 0/Major 2.5/Miner 4.0 corresponds to the maximum acceptable number of defects are 0/10/14.
That is to say, the sample size of goods shall be 200 pcs, the maximum allowed Critical defect is 0, Major defects are 10 and Minor defects are 14.
Inspection Level divided into S1, S2, S3, S4, I, II and III, and the further to the right the larger sampling amount, we can choose Level II for general goods.
AQL value divided into 0, …1.0, 1.5, 2.5, 4.0, 6.5, …, and the further to the right the larger number of acceptable defects, which means lower requirements for quality.
Take an example, the quantity of a batch of goods is 7,500 pcs, if we use Inspection Level II, and AQL Critical 0/ Major 2.5/ Minor 4.0.
Step 1: total 7500 pcs can be find the Lot Size is 3201-10000.
Step 2: find the general Inspection Level is L.
Step 3: find L in Sample Size Code Letter and the Sample Size is 200.
Step 4: on the right of this string, AQL Critical 0/Major 2.5/Miner 4.0 corresponds to the maximum acceptable number of defects are 0/10/14.
That is to say, the sample size of goods shall be 200 pcs, the maximum allowed Critical defect is 0, Major defects are 10 and Minor defects are 14.
How to establish the reasonable AQL standard for your product?
AQL is the boundary of acceptable and unacceptable and is a parameter relevant to sampling scheme. In order to determine the appropriate AQL value, some principles that can be followed are listed below. However, so far there has not been a method applicable under all different circumstances.
Consider the purpose of products and the consequences due to product failure. For example, for electronic components of the same specification, the AQL value for equipment for civil use could be higher than that for military equipment, and the AQL value for general products could be higher than that for precision products.
Consider the cost, the AQL value shall not be too low, otherwise the production cost and inspection cost will be increased, or the goods will be rejected frequently, which results in loss of both the buyer and seller.
For goods in urgent need of clients, if the manufacturer cannot improve the quality within a short time and in order to receive goods timely, AQL value has to be higher as appropriate, and by the time the manufacturer improves the quality, AQL value could be adjusted.
If there’re many components of a product and the unqualified components are easily found and replaced by qualified components at the time of assembly and maintenance, AQL value could be higher, and vice versa.
At the time of establishing AQL value, consider the average of the quality supplier may offer and the ideal quality the consumer thinks, in other words, the average of the expected quality of consumers and the quality they could afford, due to the added expenses on production cost and inspection cost for the purpose of improving quality are ultimately included in product price.
For some household appliances, clothes and consumer goods, if the poor performance or function is due to unreasonable product design, manufacturing technology or raw materials (Major defects), AQL value should be lower. For defects having influence only on appearance of products, such as scratches, untrimmed thread, etc., AQL value could be higher.
Consider the purpose of products and the consequences due to product failure. For example, for electronic components of the same specification, the AQL value for equipment for civil use could be higher than that for military equipment, and the AQL value for general products could be higher than that for precision products.
Consider the cost, the AQL value shall not be too low, otherwise the production cost and inspection cost will be increased, or the goods will be rejected frequently, which results in loss of both the buyer and seller.
For goods in urgent need of clients, if the manufacturer cannot improve the quality within a short time and in order to receive goods timely, AQL value has to be higher as appropriate, and by the time the manufacturer improves the quality, AQL value could be adjusted.
If there’re many components of a product and the unqualified components are easily found and replaced by qualified components at the time of assembly and maintenance, AQL value could be higher, and vice versa.
At the time of establishing AQL value, consider the average of the quality supplier may offer and the ideal quality the consumer thinks, in other words, the average of the expected quality of consumers and the quality they could afford, due to the added expenses on production cost and inspection cost for the purpose of improving quality are ultimately included in product price.
For some household appliances, clothes and consumer goods, if the poor performance or function is due to unreasonable product design, manufacturing technology or raw materials (Major defects), AQL value should be lower. For defects having influence only on appearance of products, such as scratches, untrimmed thread, etc., AQL value could be higher.